Now that we’re back in the studio blowing glass, we’ve decided to go big or go back home. This week we got to work with our large reheating chamber. We don’t get to use this beast very often, so we thought it was a great time to fill you in on when we use it and what we make with it. Keep reading to find out about this exciting piece of equipment we’re so lucky to have.
The Specs
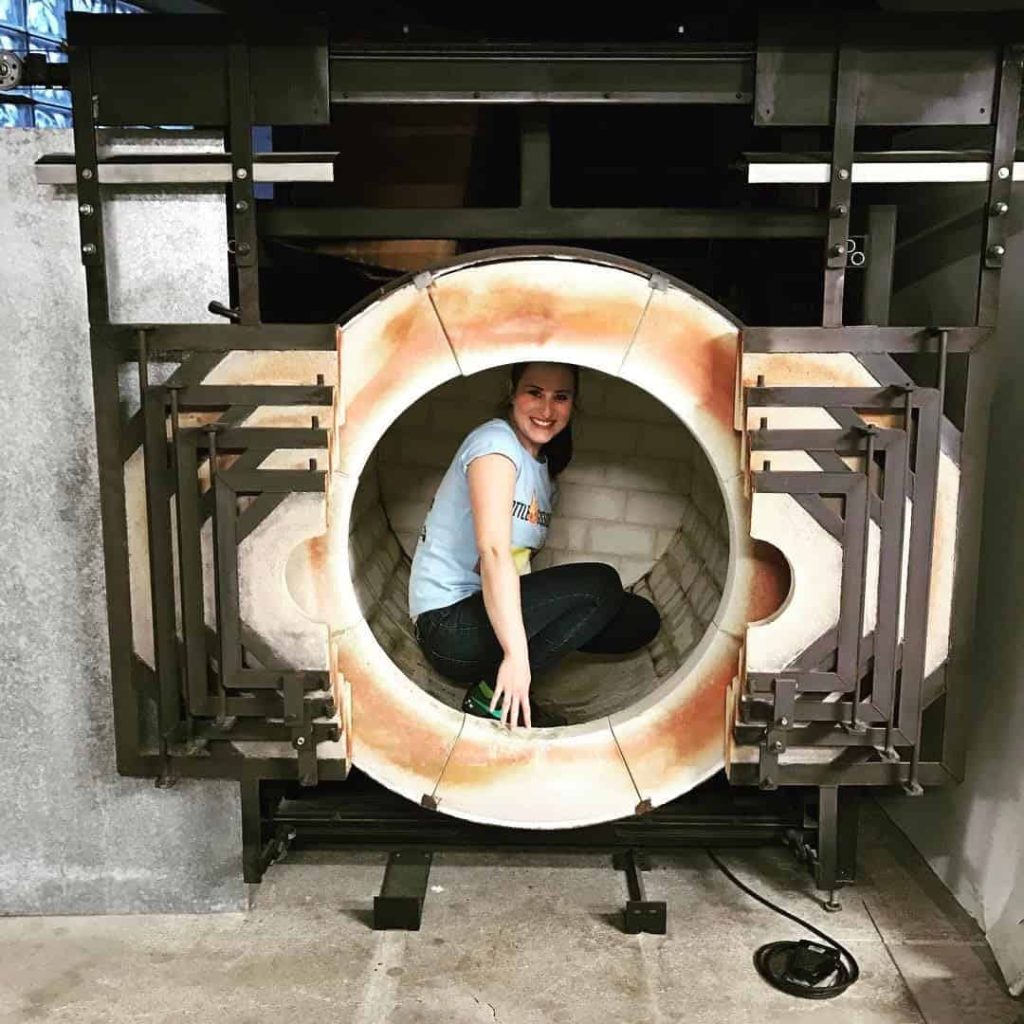
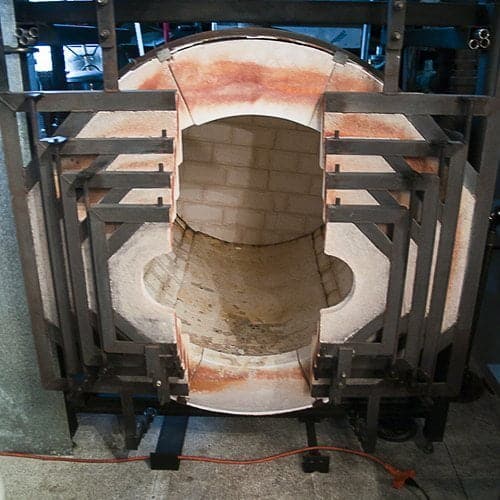
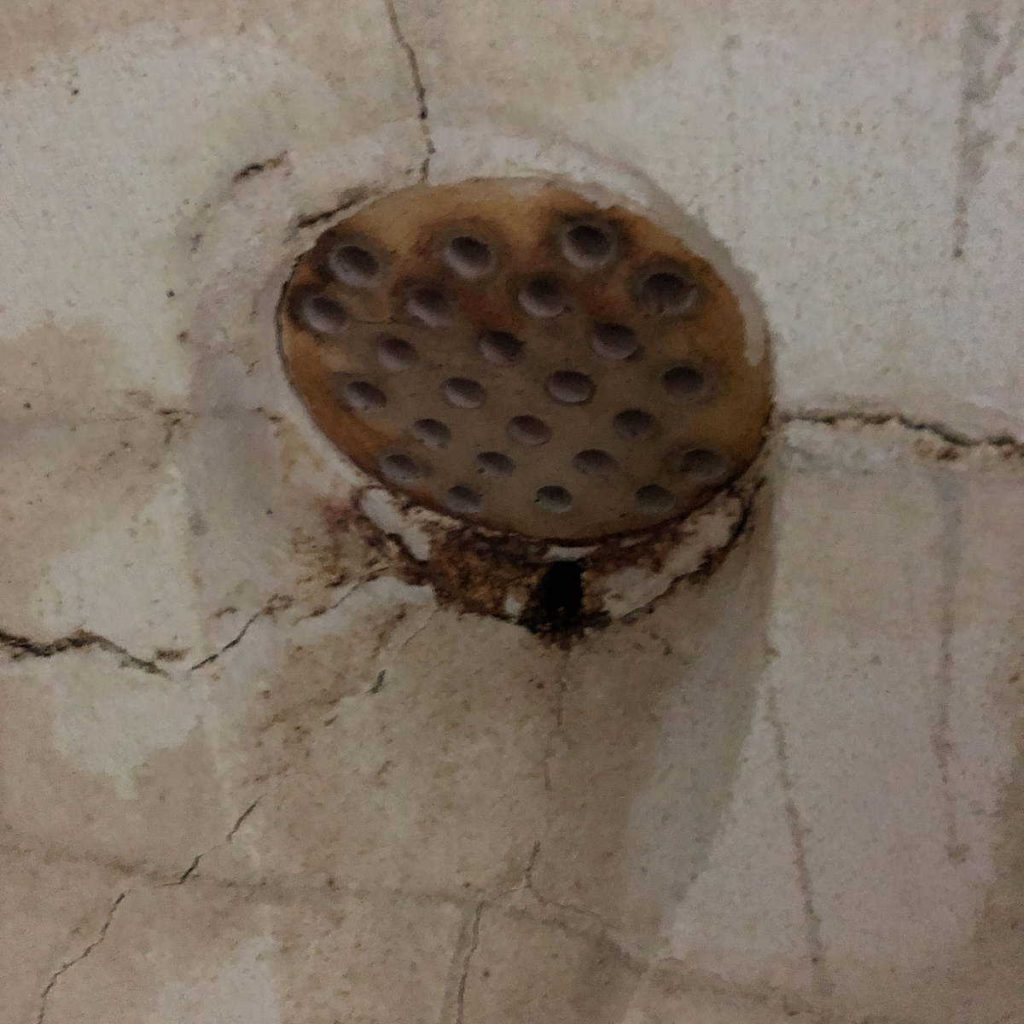
So just how big is our large reheating chamber? It’s 52″ x 41″ or approximately 4.33′ x 3.341′. Big enough for Becca to fit in as you can see above! And it’s actually the largest reheating chamber in all of Michigan.
This monster runs 2400 degrees Farenheit – so it’s REALLY HOT. And there’s no escaping the heat as it fills the whole studio. So as you can imagine we don’t work out of it in the summer, but in the winter it makes the cold days warm right up!
The reheating chamber has four burners (see above right) that burn at 1.5 million BTUs per hour. These burners use forced air/natural gas. It takes about one hour to get up to working temp and we work out of it for 6 hour slots. The chamber also has four sets of doors. We start out with the smallest set of doors and as the piece gets larger, we open up the larger doors to accommodate.
Take a look at the infographic below for the major differences between the large and small reheating chambers. The small one is used on a day-to-day basis. The larger one is used on occasions when we have a special large-scale project.
What’s working with the reheating chamber like?
When we work with this reheating chamber, we need the whole team to help. This means 5-6 people all working together all with different tasks. The gaffer is the head of the team, taking direction from the artist unless s/he is the artist. Assistants help with prepping bits and bringing them over, opening and closing the doors of the reheating chamber, shielding each other from the heat of the glass, turning, lifting and shaping, torching and anything else that needs to be done in the moment.
As you can imagine this is a really intense experience with a lot going on at the same time! All of these people need to work together like a well-oiled machine. A great team is imperative and we’re lucky to have just that. Watch the video below to see some of the action.
What Makes it More Challenging?
Pretty much everything! Teamwork and communication are key. It takes a long time to develop a good team because parts of process significantly different than when you work at smaller scale. We’re lucky to have a great team that can work together under pressure to make these large-scale pieces.
Factors that make things more difficult are weight, torque and heat. These are big pieces that are heavy on their own. Holding them on the pipe up to four feet from your body causes that weight to double with each foot. So, a finished 20 lb. Splash Bowl on a 4 ft. pipe will feel to be about 60 lbs including scrap glass and the pipe. But because of torque, centripetal motion and the fluidity of glass, it’s unstable. Instead of feeling like a 60 lb. rock, it feels like 60 lbs of Jell-O because the glass moves. You have to keep this heavy unstable molten glass constantly in motion so it doesn’t fall. There is resistance from this constant turning and if the glass goes off center, it will feel even heavier. It’s a lot to take in all and once – and it’s not all!
Heat, Safety & Failure
The reheating chamber and the glass we’re working with are so large. The piece might be 1200 degrees Farenheit while it’s being moved between the reheating chamber and the bench or the marver. There’s a lot of radiating heat. Because of this, the glass artists have to use protective gear like Kevlar sleeves (the yellow sleeves you see them wearing above), gloves, face shields and even wooden paddles to shield themselves and each other. We even have a crazy space suit that you can see at the right. This protects from the radiant heat when putting a piece in the annealer after it’s knocked off the pipe.
To give you an idea of just how hot this heat is – if you breathe it in, you can burn off your nose hairs! When recording videos of the artists working on an iPhone, a message came up saying the phone needed to cool down though it was never closer than a foot from the glass. So, it’s definitely a heat you can feel.
Lastly, sometimes things just don’t go as planned. It’s a lot of time, materials and energy to put in to a single piece. We can only make 3 – 4 at most in one day. And sometimes they end up like the bubble light to the right. But we just try, try again. It takes a lot of problem solving, patience and perseverance.
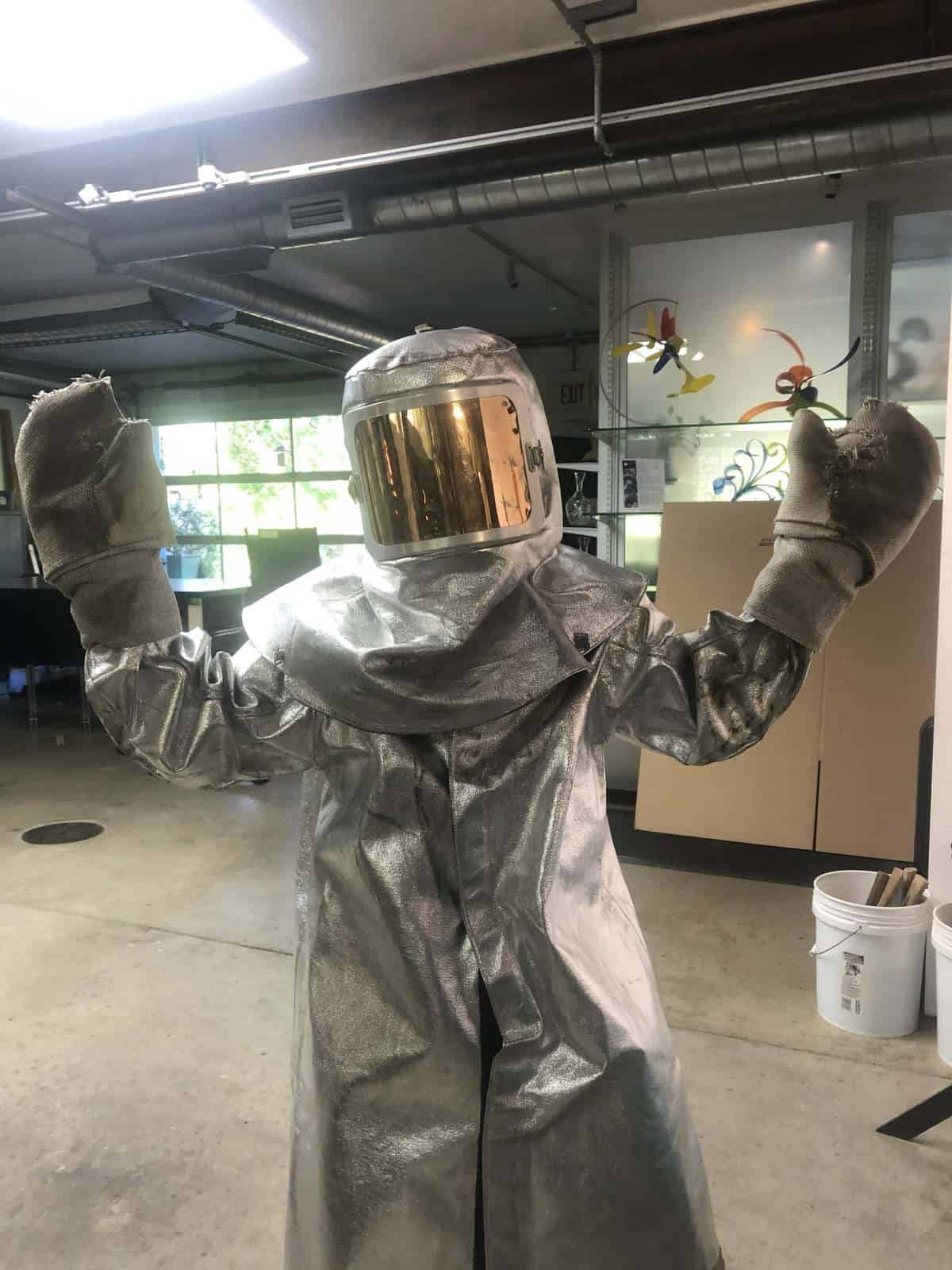
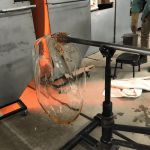
What do you make with it?
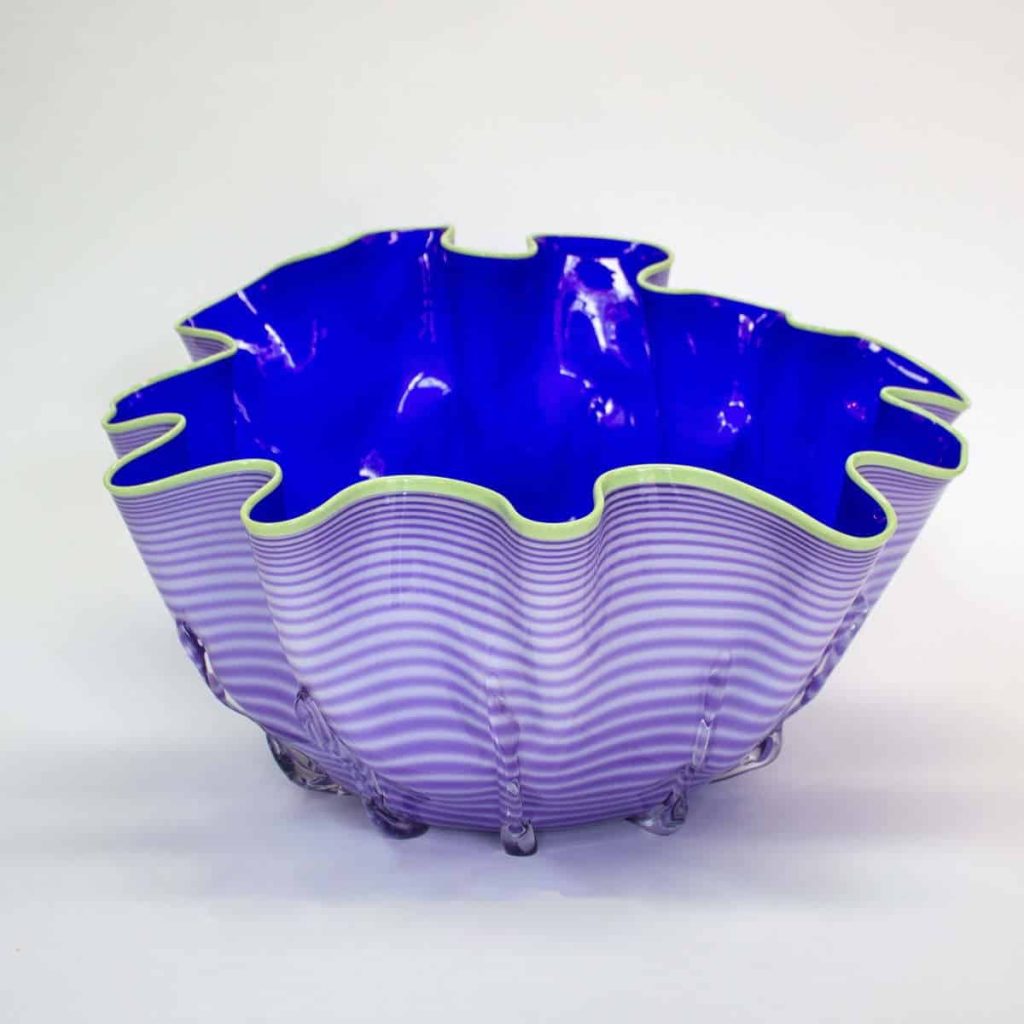
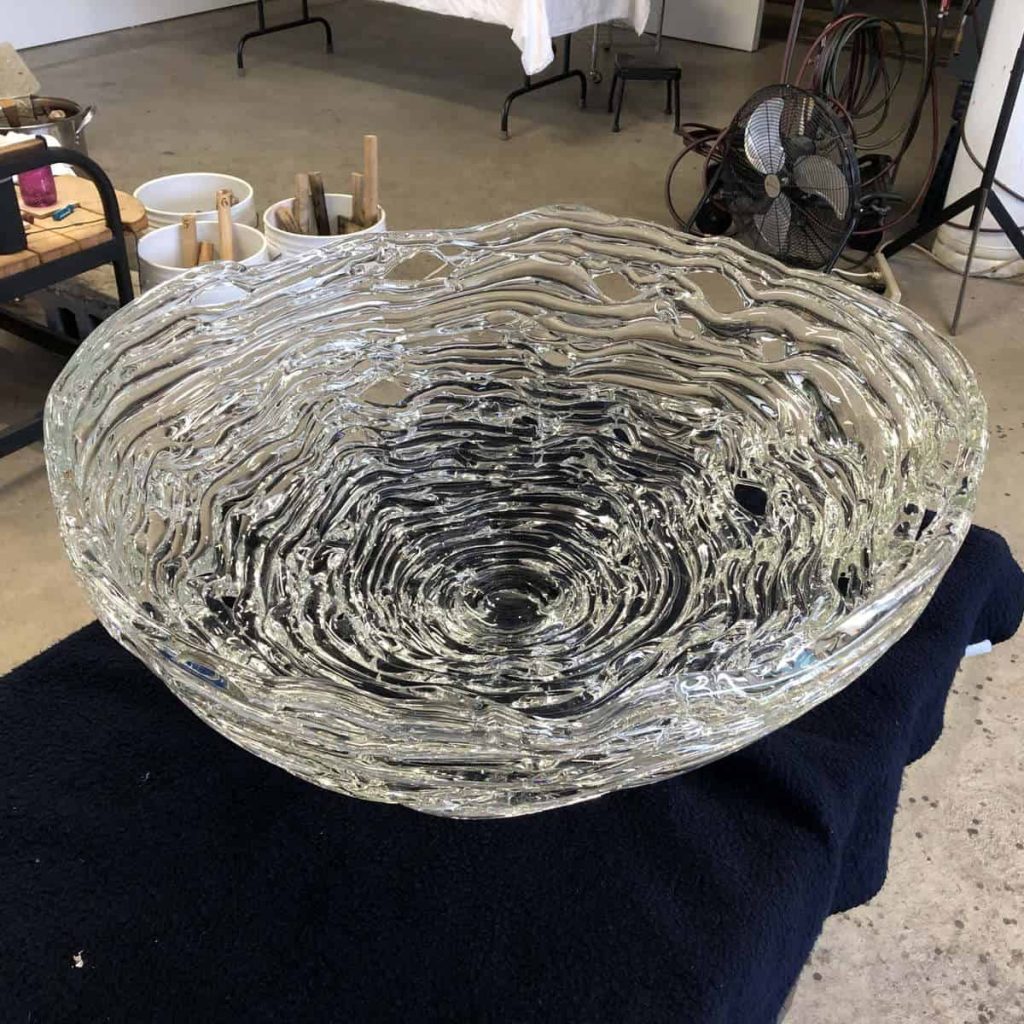
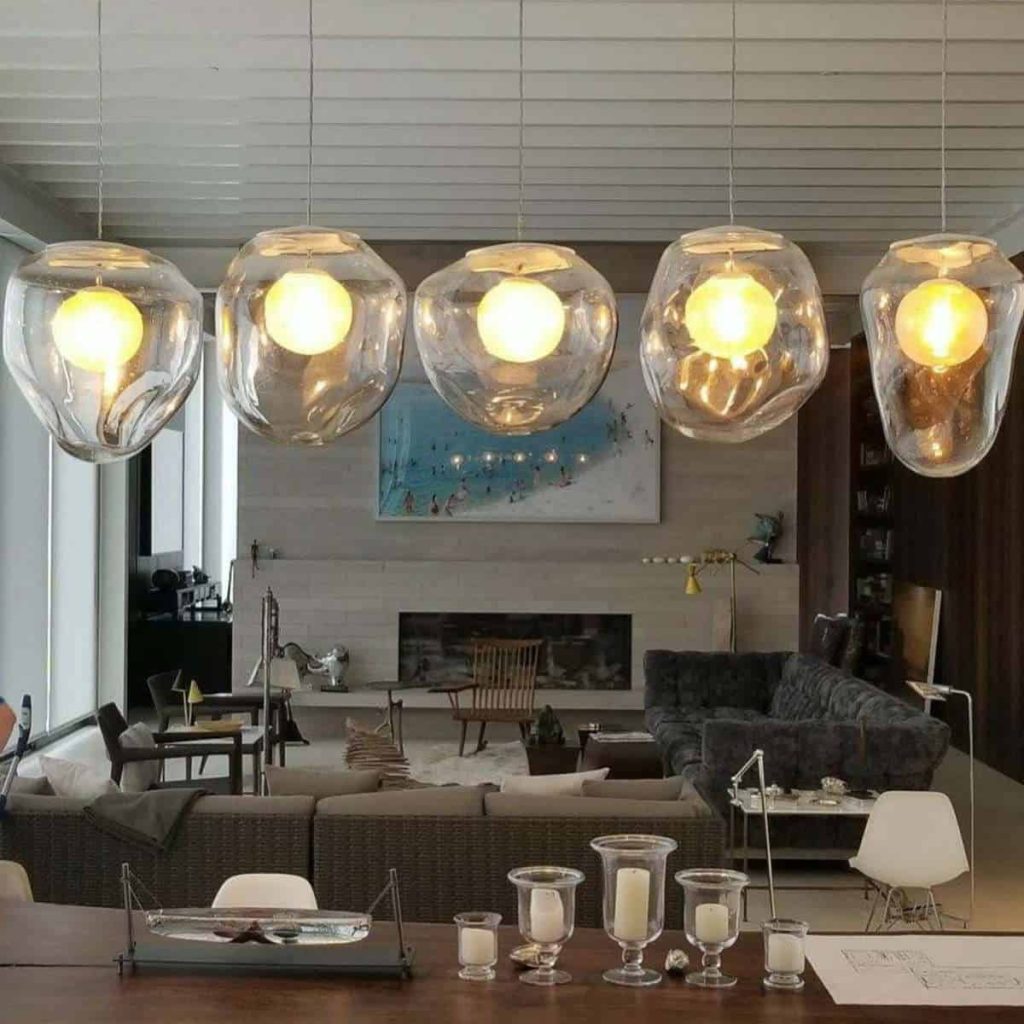
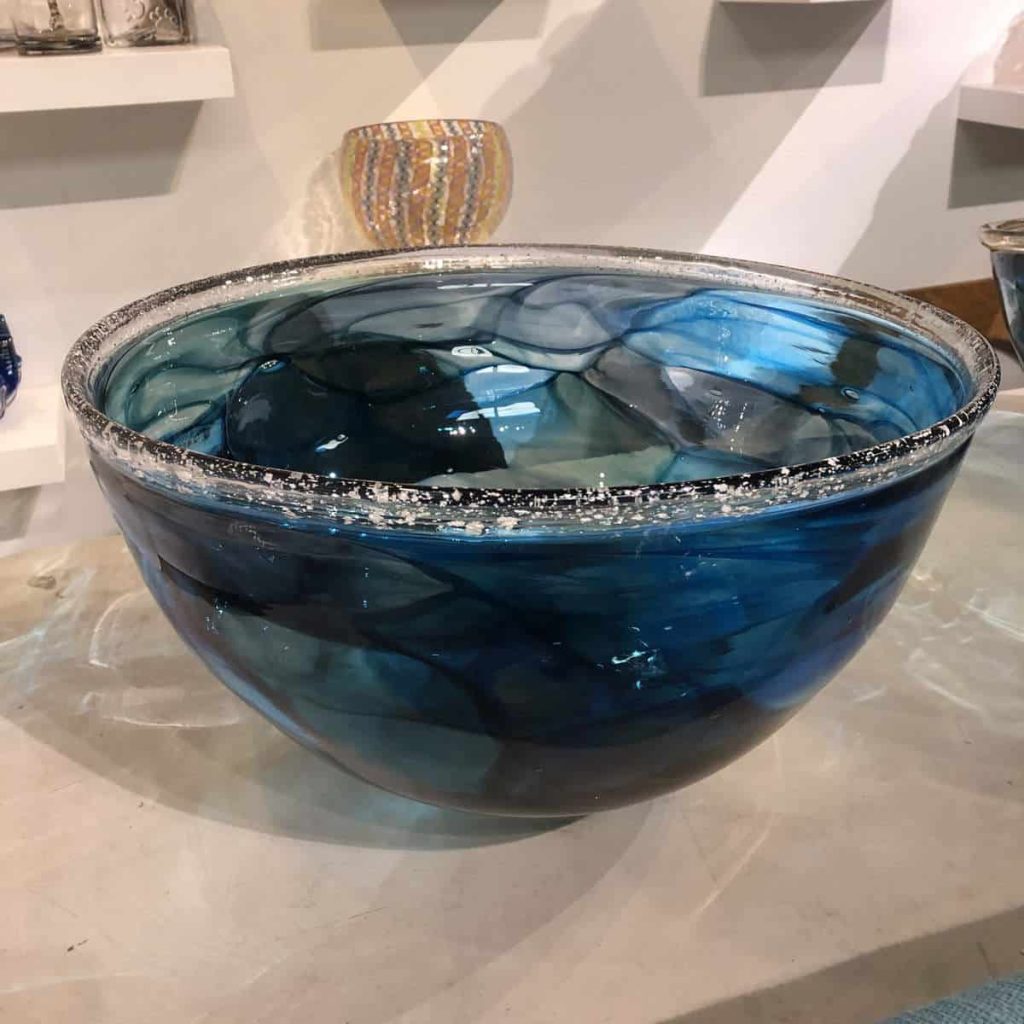
So what do we make using the large reheating chamber? Large scale artwork! Above are just a few of the examples of pieces we’ve made.
- Large Splash Bowls – you may recognize our signature Splash Bowls. We made a series of large ones that are between 1.5 – 2′ in diameter. If you didn’t already watch the video above, go check it out now to see how they’re made. You can pick up one of our large Splash Bowls in our shop.
- We made these beautiful coiled light fixtures. Unfortunately, the design didn’t work out in the end because they kept cracking. But we loved the organic beehive look and they inspired what would become our La Ruche lighting line.
- This series of bubble lights was a special commission for a private residence. The failed piece above is one of these lights. Like we said before – working large takes patience and you have to move through some fails to reach a success.
- These are our most recent large-scale pieces. A local church commissioned us to make these beautiful baptismal sinks. We love the swirling colors and are so happy with how they turned out.
We hope this gave you an interesting look at what goes into creating our large-scale works. We’d like to leave you with one other video showing how we made the coiled light fixture above. This piece is a bit different as it’s sculpted rather than blown.
As always, you can keep up-to-date with us on Facebook, Instagram (which you love if you enjoyed the videos in the post!) or by signing up for our weekly newsletter.
Thanks for reading and if you have questions, please feel free to leave them in the comments below!